ALUCORE® can be joined by means of standard processes used in metal and plastics technology. If ALUCORE® is to be joined to structural parts of metals other than aluminium, or if fasteners (e.g. bolts, screws) are to be used, the following material guidelines should be observed:
Fasteners and structural parts made of aluminium, plastic or stainless steel should be suitable for assembly with ALUCORE®. When using other materials, please insert insulating washers or apply a protective coating to prevent corrosion.
Please take the thermal expansion of the panel into account for outdoor use of ALUCORE® to avoid jamming or deformation. The minimum gap depends on the expected expansion of the panel. Please refer to processing recommendations for rivets and bolts for additional measures to prevent jamming. The linear thermal expansion of ALUCORE® is determined by the aluminium cover sheets. At a temperature difference of 100°C the longitudinal deformation is 2.4 mm/m length/width.
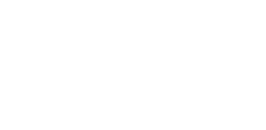
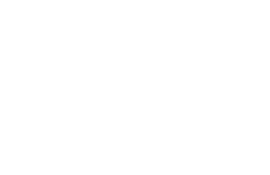
Rivets – not penetrating the panel
Rivets generally must be anchored in the 1mm thick ALUCORE® cover sheets. Sections can be attached to ALUCORE® with commercially available rivets for aluminium constructions. After drilling a blind hole of the same diameter as the rivet shank, the rivets can be anchored in the cover sheet. As a rule, rivets with stainless steel mandrel are used.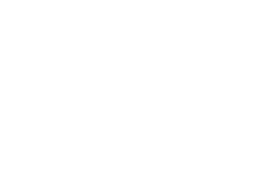
For outdoor use please note:
- For outdoor use aluminium blind rivets that have been approved for construction with a 5 mm shaft diameter and an attachment head diameter of 11 or 14 mm are used.
- Please take the thermal expansion of the panel into account (2.4 mm/m/100°C). To avoid jamming, the hole in the panel must be large enough to allow for expansion.
- With the shaft of the rivet fitting closely to the edge of the hole, the attachment head must cover over 1 mm of the area surrounding the hole.
- Multi-step drills or sleeves having corresponding diameters are used for centrically drilling holes into the panel and the substructure and for centrically fitting the rivet.
- Rivet attachment jigs are used for fitting blind rivets without jamming allowing for a tolerance of 0.3 mm. Make sure to use rivet attachment jigs and rivets from the same manufacturer, as the height of the attachment head according to DIN 7337 may vary.
- The clamping thickness results from the thickness of the material to be riveted plus an additional value of 2 mm to ensure that the closing head is perfectly formed. In accordance with this clamping thickness the corresponding shaft length is determined in the tables provided by the rivet manufacturers.
Important: during riveting many factors may have an influence on the exact tolerance of the rivets of 0.3 mm (e.g. rivet head tolerance), we recommend that you make a test on a fascia panel. Please always remove the protective foil in the riveting area prior to riveting.There are various types of rivet heads and materials which can be selected depending on the intended application. The blind rivet nuts or bolts are inserted in blind holes drilled in one side of the ALUCORE®panel. Subsequent fitting with a tool is fast and cost-effective. (See Fig.) Due to the minimum shaft length of 11 mm these fixtures can only be used for a panel thickness of 15 mm or more. As a rule, the rivet must be anchored in the 1 mm thick cover sheet.
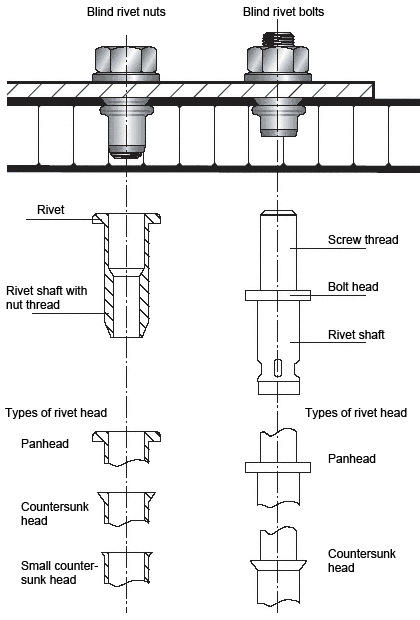
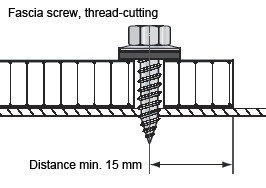
Threaded fasteners for outdoor use
For outdoor use make sure to take the thermal expansion of the panel into account. To avoid jamming, the hole diameter in the panel must allow for the expansion. Fastening without jamming is possible using fascia screws made of stainless steel with sealing washer (Fig. 1) that have been approved for construction. The screws must be suitable for the corresponding substructure (please note the information given by the manufacturer). The screws should be tightened with a torque wrench or screwdriver so that the sealing washer is placed on the panel for sealing the bore hole without exerting pressure to the panel. Multi-step drills or sleeves having corresponding diameters are used for centrically drilling holes into the panel and the substructure and for centrically fitting the rivet. Important: Make sure to remove the protective foil prior to screwing.Examples for threaded fasteners
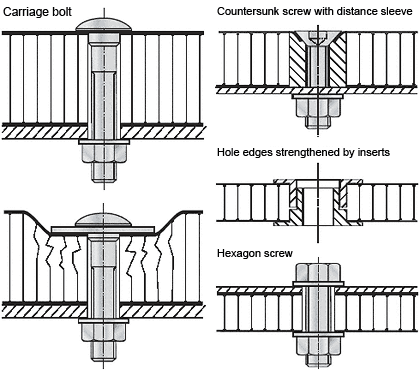
Stud welding with tip ignition on mill-finished ALUCORE® surfaces Process:
- The capacitor battery is charged.
- A spring in the welding gun moves the stud (with tip) towards the work-piece.
- The tip comes into contact with the work-piece and thereby closes the circuit. The rapidly increasing current causes the ignition tip to melt instantaneously, thus initiating the electric arc.
- Stud and work-piece are welded together.
- When the stud touches the work-piece the electric arc is extinguished, the fusion zones on stud and work-piece are joined and solidify.
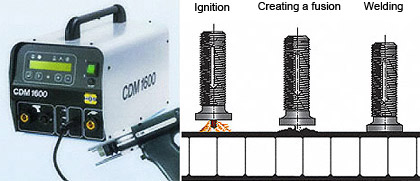